ASN Wikibase Occurrence # 297847
This information is added by users of ASN. Neither ASN nor the Flight Safety Foundation are responsible for the completeness or correctness of this information.
If you feel this information is incomplete or incorrect, you can
submit corrected information.
Date: | Wednesday 26 June 2019 |
Time: | 21:33 LT |
Type: | Beechcraft E55 Baron |
Owner/operator: | Industrial Power Inc |
Registration: | N664AR |
MSN: | TE-1163 |
Year of manufacture: | 1979 |
Total airframe hrs: | 2178 hours |
Engine model: | Continental IO-520 |
Fatalities: | Fatalities: / Occupants: 3 |
Aircraft damage: | Destroyed |
Category: | Accident |
Location: | Hope Mills, North Carolina -
United States of America
|
Phase: | Approach |
Nature: | Private |
Departure airport: | Fayetteville Regional Airport, NC (FAY/KFAY) |
Destination airport: | Fayetteville Regional Airport, NC (FAY/KFAY) |
Investigating agency: | NTSB |
Confidence Rating: | Accident investigation report completed and information captured |
Narrative:Three days before the accident flight, the accident pilot flew two friends/pilots on a cross-country flight in the accident airplane. According to one of the friends, during the first leg of that trip, the attitude and heading reference system (AHRS) fail amber caution light illuminated in the cockpit at engine startup and remained illuminated for 12 to 15 minutes, which included the initial portion of the flight. They discussed continuing the flight under visual flight rules because the autopilot would not engage with the caution light illuminated and would not remain engaged if the caution light illuminated. During the time the caution light was illuminated, no anomalies were observed with the electronic flight information system (EFIS) display. The caution light extinguished, and the accident pilot engaged the autopilot for the remainder of the flight leg. During the return flight, the light remained extinguished and the accident pilot used the autopilot; however, after landing, he turned off the avionics and then back on, and the light illuminated for 3 minutes before he shut down the airplane. He planned to take the airplane to an avionics maintenance facility and also commented that he planned to perform three night landings to maintain his night currency.
On the evening of the accident flight, the accident pilot visited the maintenance facility and was informed that the repair related to the AHRS fail light illumination had not been completed because the facility needed to contact the EFIS manufacturer for more information. The accident pilot elected to fly the airplane without the repair having been completed.
The accident flight was cleared for takeoff, and about 2 minutes later, the pilot reported a problem to air traffic control but did not specify what the problem was; he stated that he wanted to turn around and land. but the pilot noted that there was an 'awful lot of control wheel weight.†The flight was cleared to land, and the pilot subsequently stated, "it's really wanting to pitch down bad for some reason." A witness, who was walking his dog at the time, reported seeing the airplane veer sharply, followed by a steep descent about a 45° angle, just prior to impact. The airplane subsequently impacted a residence and terrain about 2 miles southwest of the approach end of the runway.
Examination of the engines did not reveal any preimpact mechanical malfunctions and flight control continuity was confirmed. Examination of the autopilot programming unit and engine monitor revealed that they did not contain any nonvolatile memory. The investigation could not determine if the pilot was troubleshooting or attempting to use the autopilot during the accident flight.
Postaccident testing of the clutch tension of the pitch servo revealed the breakaway force needed was 45 lbs. However, the specified required clutch tension breakaway force setting was 13 /- 2 lbs. This setting was achieved by tightening the castle nut enough to reach the required force. After that, an orange torque seal strip was applied and a cotter pin was installed. Further examination revealed that the cotter pin used to secure the castle nut retaining the clutch appeared to be new, and the castle nut did not align with the factory orange torque strip setting applied at the time of servo completion and final testing. The orange torque strip on the nut and the orange torque strip on the tension washer were about 3/4 of a turn off. At some point during previous maintenance, the castle nut securing the clutch on the servo was overtightened, which caused the breakaway force needed to be 30 lbs over the specified limit. The overtightened clutch would have greatly increased the force required to override the clutch of the pitch servo.
The pilot operating handbook for the airplane make/model indicated that an uncommanded pitch could be stopped by: turning off the autopilot master switch; pull the autopilot and trim circuit breakers; turn off the radio master switch; turn off the electrical master switch; push the GA switch on the throttle grip; or push TEST EACH FLT switch on autopilot controller..
Probable Cause: The pilot's failure to disengage an uncommanded nose-down pitch input. Contributing to the accident was improper maintenance of the pitch trim servo, which would have precluded a physical override of the pitch servo.
Accident investigation:
|
| |
Investigating agency: | NTSB |
Report number: | ERA19FA201 |
Status: | Investigation completed |
Duration: | 1 year and 5 months |
Download report: | Final report |
|
Sources:
NTSB ERA19FA201
Location
Revision history:
Date/time | Contributor | Updates |
15-Oct-2022 09:24 |
ASN Update Bot |
Added |
The Aviation Safety Network is an exclusive service provided by:
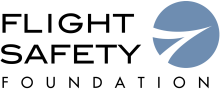
CONNECT WITH US:
©2024 Flight Safety Foundation