ASN Wikibase Occurrence # 209447
This information is added by users of ASN. Neither ASN nor the Flight Safety Foundation are responsible for the completeness or correctness of this information.
If you feel this information is incomplete or incorrect, you can
submit corrected information.
Date: | Thursday 1 February 1996 |
Time: | 12:30 |
Type: | Ayres S-2R-R1820 Bull Thrush |
Owner/operator: | |
Registration: | VH-BRN |
MSN: | R1820-016DC |
Fatalities: | Fatalities: 0 / Occupants: 2 |
Aircraft damage: | Substantial |
Location: | 30km E of Canberra Airport, NSW -
Australia
|
Phase: | Manoeuvring (airshow, firefighting, ag.ops.) |
Nature: | Survey |
Departure airport: | YSCB |
Destination airport: | YSCB |
Investigating agency: | BASI |
Confidence Rating: | Accident investigation report completed and information captured |
Narrative:The aircraft had recently been returned to service following major modification and restoration work. This included the replacement of the piston engine with a Garrett gas turbine engine. The purpose of the flight was to allow the pilot to familiarise himself with the handling characteristics of the aircraft. Another pilot, who had considerable experience on the aircraft type, occupied the passenger seat behind the pilot seat to advise the pilot on methods of operating the aircraft during various manoeuvres. Following departure to the training area at approximately 1230 EST, the pilot commenced agricultural type procedure turns at 6,500 ft, which included a manoeuvre similar to a wingover. He recalled observing an indication of 1,200 degrees Celsius on the inter-turbine temperature gauge whilst the aircraft was in a nose-high attitude at the top of a wingover to the left. This indication exceeded the engine temperature limit. Shortly after, he saw the inter-turbine temperature reducing through 300 degrees Celsius and assessed that the engine had failed. He was unable to remember specific actions he had taken in attempting to restore power to the engine but believed he had made some effort to do so. A checklist had not been referred to during this flight for either normal or emergency procedures. The pilot recalled that, following the loss of power, the airframe was buffeting with little or no response to his control inputs. During the subsequent descent, the aircraft struck the top of a tree before colliding with the ground in a steep nose-low attitude. Both occupants sustained serious injuries. The passenger reported that the takeoff was completed with the speed lever (engine RPM control) intentionally left in the low-RPM position for demonstration purposes. He did not remember whether the speed lever was returned to the correct operating position after takeoff; however, he believed the pilot had done so. The passenger's first recollection of the inter-turbine temperature gauge was a low temperature followed by an over temperature condition which he observed in the ensuing descent. (This observation conflicts with the pilot's report.) He also believed he may have given instructions that were intended to assist the pilot in his attempt to restore engine power. Personnel information Pilot The pilot held a current licence which was valid for the operation being undertaken. He held a class endorsement which permitted him to operate Ayres Thrush or Air Tractor aircraft fitted with either a Garrett or a Pratt and Whitney PT6 gas-turbine engine. The aircraft used for the endorsement was an Ayres Thrush fitted with a Pratt and Whitney PT6 engine. The endorsement included 1.5 hours of ground instruction covering normal and emergency procedures and 2.5 hours of flight time, flown as solo practice because the aircraft used for the endorsement was equipped with only one seat. The pilot recalled practising general handling of the aircraft, including stalls and circuits. No simulated emergency procedures were practised in flight. Having completed the endorsement on 28 January 1996, the pilot flew 2 hours in the accident aircraft, consisting of three separate flights in which he practised general handling, including circuits. No simulated emergency procedures were practised during these flights. Passenger The passenger was a licensed pilot with an agricultural rating. He had considerable experience in Ayres Thrush aircraft equipped with Garrett gas turbine engines and was considered by his associates to have a sound knowledge of the aircraft's systems and handling procedures. Input from the passenger during the flight was limited to instructions and advice administered through the intercom system because his seating position permitted only restricted forward vision and the aircraft was not equipped with dual controls. Aircraft information The Ayres Thrush is a low-wing, tailwheel landing gear aircraft used primarily in agricultural operations. Supplemental Type Certificate SA00172SE, to enable installation of a Garrett gas-turbine engine, was approved by the Federal Aviation Administration on 17 February 1995 and was validated by the Civil Aviation Safety Authority. The installation in this aircraft was the first of its kind in Australia fitted in accordance with the supplemental type certificate. Prior to overhaul, the aircraft had accumulated a total of 2,472.8 airframe hours. The maintenance release was signed on 17 November 1995, following engine installation and aircraft refurbishment. Approximately 3 hours flight time, including 14 engine cycles, was noted on the maintenance release prior to the accident flight. Engine The engine was a Garrett TPE331-6-252M gas-turbine engine. It had accumulated 5,614.1 hours total time, including 8,421 cycles, prior to an overhaul carried out at the Garrett engine division of AlliedSignal in Phoenix, Arizona. It was installed in the Ayres Thrush airframe following shipment to Australia in November 1995. The engine utilises two control levers: one is known as the speed lever and controls the engine RPM, while the other controls the fuel to the engine and is known as the power lever. The power lever also gives the pilot control over the propeller pitch angle during ground operations (beta mode). During normal operations, the speed lever is selected to the high-RPM position for takeoff and climb so that maximum power is available. In cruise, or whilst manoeuvring, the pilot may choose to leave the speed lever in the high-RPM position or, to achieve better fuel economy and reduce noise, select 96% RPM. Reports from pilots experienced on the aircraft type suggest there have been occasions when the speed lever has been inadvertently left in the low-RPM position for takeoff, resulting in degraded take-off and climb performance. The engine speed lever is linked to the underspeed fuel governor and the propeller governor. If the speed lever were left in the low-RPM position in flight and the power lever moved toward the flight idle position during a manoeuvre such as a wingover, the speed of the engine would remain constant at about 94%, as a function of the propeller governor. This would continue to be the case until the aircraft's speed reduced to within a few knots of the stall speed. At this point, the engine RPM would decay towards the underspeed fuel governor setting of about 70% due to the decreased fuel demand and propeller load. If the power lever were then advanced, the engine would experience a "bog down" situation in which the loading on the engine results in a decay of engine RPM. In the situation described, the bog down is due to an overfuel condition caused by the power lever commanding an excessive amount of fuel to the accelerating engine. This would be accompanied by high localised temperatures and a possible flameout due to the interruption of combustion resulting from a poor fuel/air ratio. Propeller The Hartzell propeller assembly was three-bladed, fully reversible and feathering, model HC-B3TN-5M. It was fitted to the aircraft as new on 7 November 1995. To facilitate the engine ground start, the power lever should be in the ground-idle position with the propeller blades resting against the start lock pins. Once engine parameters have stabilised, the propeller can be released from the start locks by moving the power lever towards reverse. During engine shutdown, the propeller start locks re-engage when engine RPM is less than 50%. The shutdown procedure calls for the power lever to be placed into the reverse range before the engine RPM reduces below approximately 50%. If the pilot does not make the selection before this time, there will be insufficient oil pressure in the propeller dome to force the blades into the reverse position before the start lock pins engage. The installation prohibits the use of reverse thrust in flight and must comply with United States Federal Aviation Regulation (FAR) 23.1155 which states that "each control for reverse thrust and for propeller pitch settings below the flight-idle regime must have means to prevent its inadvertent operation". The flight control quadrant on this aircraft provides a detent at the flight-idle position. The movement of the power lever rearward of the flight-idle detent is positive but requires only light pressure to lift the latches, located under the head of the power lever, and to move the lever rearwards. A negative torque sensing system is provided on the engine. Negative torque sensing reduces excessive aerodynamic drag on the propeller in the event of an engine malfunction or failure by modulating the mean blade angle towards feather. However, the negative torque sensing system is not an automatic feather system. The process is immediately effective and will move the blades, by increments, to a position corresponding to approximately 90% of the fully feathered position. The pilot's operating handbook for TPE331 engines states that if the propeller is not manually feathered before the engine RPM decays to 30%, propeller RPM will stabilise and continue to rotate at some RPM below 30% for as long as forward airspeed is maintained. The negative torque sensing system fitted to the aircraft has been certified in accordance with FAR 23.937 which implies that, in the event that the negative torque sensing system fails to operate correctly, the pilot is still able to maintain control of the aircraft, albeit with significantly more drag due to a windmilling propeller. It is understood that this has been demonstrated during the original certification process. The aircraft was therefore not required to be fitted with manual feathering capability which allows the pilot to manually select the propeller blades to the feathered position. The aircraft flight manual states that a negative torque sensing system functional check should be performed on the final engine shutdown of the day. There were no reported problems when functional checks were carried out during ground and flight tests following the installation of the engine. On the 3 days preceding the accident flight the pilot was the only person who had flown the aircraft. He did not recall carrying out a negative torque sensing system check at the completion of any of the three flights he had undertaken during that time. Engine fuel control system A Woodward fuel control unit was installed in the aircraft. The unit is a mechanical device and provides a pressurised source of fuel to the engine under all operating conditions. It was overhauled and inspected, in accordance with Federal Aviation Administration airworthiness regulations, on 23 February 1995 then shipped to the Garrett engine division of AlliedSignal in Phoenix, Arizona. Extra fuel is metered to the engine during start-up and engine acceleration. The P3 line provides a reference pressure for acceleration fuel scheduling during these times and is located externally between the engine compressor and the fuel control unit. If the P3 line were to become partially blocked, power response could be unpredictable, ranging from a slowness of acceleration to no observed adverse response. If there were a 100% blockage of the P3 line which occurred during operation of the engine at some intermediate engine speed, such as 96%, and the speed lever was then advanced to 100%, there would be no adverse effect unless the power lever was then advanced sufficiently to require a higher fuel flow than the acceleration schedule currently set. If this were to occur, there would be a possibility of a fuel-limited condition accompanied by a slowness of engine acceleration, and all engine parameters would begin to fluctuate. These fluctuations, if left uncorrected, should become greater in magnitude with time; however, a reduction in power should stop the increase in the fluctuations. A blockage of the P3 line whilst the engine was operating otherwise normally in flight would not, in itself, be sufficient to precipitate power loss or engine failure. Neither the pilot nor the passenger recalled observing or sensing fluctuations of engine parameters such as RPM, temperature, or torque leading up to the loss of power, and they believed that engine temperatures were consistent with normal operations until that time. The manufacturer, AlliedSignal, stated that with the speed lever in the low-RPM position in flight, it would not be possible to achieve an inter-turbine temperature as high as that reported by the pilot. It was considered that the model of fuel control unit fitted to the engine would not have been capable of delivering sufficient fuel to achieve such temperatures before an engine surge and flameout. Meteorological information At the time of the accident a warm air cell had just moved through the Canberra region. A large inversion was present at approximately 7,000 ft, with associated turbulence due to the temperature gradient and strong winds from the west. At 6,500 ft, the temperature was 2 degrees Celsius with a wind speed of about 40 kts. The pilot described the flight conditions at 6,500 ft as smooth with no turbulence. Wreckage and impact information The aircraft had flown through the crown of a tree before it impacted the ground in a steep nose-low attitude, approximately 30 m from the base of the tree. Cuts in the crown indicated the aircraft wings were level at that time. The propeller separated from the engine during the initial impact. All extremities of the aircraft were accounted for at the accident site. The engine was torn from its attachments, moved slightly forward and rotated to the left, and some engine controls were deformed or dislodged. The fuselage, rearward of the firewall, sustained minor damage. The cockpit area remained undeformed and was not penetrated by any part of the structure. The cabin and the pilot's seat were removed during rescue efforts. Damage to the right wing was consistent with it having collided with tree branches during the descent sequence. The left wing sustained minor damage when the aircraft struck the ground. All control surfaces were accounted for and were observed to be correctly and securely attached. The examination established continuity of control runs between the controls located in the cockpit and the individual control surfaces. No determination could be made as to the pre-impact positions of the control surfaces due to the effects of inertia and unpredictable impact-related loads. The rear part of the engine control quadrant containing the flight-idle detent was broken and pushed backwards, consistent with force having been applied through the power lever as it was moved rearwards during the impact sequence. It was determined that breakage of the quadrant and the position of the levers were consistent with the engine dislocation at impact. The instrument panel was mostly undamaged. The pre-impact settings of toggle switches and circuit breakers could not be determined. No abnormalities were observed during the external engine examination. All fracture surfaces were the result of overload due to ground impact. The engine and its accessories were removed from the accident site for further examination. Aircraft systems examination Soil, dust and finely chopped wood particles were found in the engine combustion chamber, particularly in the fuel nozzle openings. There was no indication of uneven fuel spray pattern or burning conditions, nor any evidence of heat stress within the combustion chamber. The turbine disc blades and their guide vanes contained no evidence of damage or heat-related stress. Two inter-turbine temperature probe tips were deformed by heat whilst the remaining ten probes were free of damage. The power shaft had sheared in torsional overload, indicating that the engine was turning at impact; however, the pre-impact power setting could not be determined. The P3 line was not disturbed during the initial engine examination; however, when the engine components were readied for return from the specialist examination facility to the aircraft owner, it was disconnected from the compressor plenum. A piece of red plastic, measuring about 8 x 5 x 3 mm, was found lodged in the line. This plastic was submitted to a specialist laboratory for further analysis. The investigation could not establish how the piece of plastic was introduced into the P3 line. There was no requirement for this line to be disturbed or disconnected during the installation process. No pre-existing defects which may have adversely affected engine performance were found in the fuel control unit, fuel pump or propeller governor following compliance testing and examination. Specialist examination of the propeller revealed that all blades were on the start locks. Imprints on the start lock mechanism screw faces indicated the blades were already on the start locks when the aircraft struck tree branches and the ground. No abnormality or pre-existing defect was found which was likely to have affected normal propeller function prior to impact. The aircraft had been refuelled on the morning of the accident flight and was determined to have been carrying sufficient fuel for the flight. No evidence of fuel contamination was found, and results of analysis of fuel samples taken from the aircraft and the refuelling vehicle found the fuel quality to be in accordance with specifications. All instruments were found to be serviceable prior to impact; however, pre-impact instrument indications could not be determined. Tests and research Examination of the plastic object found in the P3 line determined that it was a piece of polyester urethane type material which has many applications in aviation including tubing, O-rings, diaphragms, and gaskets. It was considered that the shape of the plastic material submitted to the laboratory was similar to a small piece cut and torn from the dome end of a solid plug or bar stock, or from the corner of a round-edged component. Analysis of the material indicated that it was capable of withstanding temperatures of up to 128 degrees Celsius. Above this temperature, softening occurred, with fusion and melting initiated at 283 degrees Celsius. It was advised by the manufacturer that temperatures of approximately 121 degrees Celsius could be expected at the fuel control unit end of the P3 line, and of up to 315 degrees Celsius at the compressor outlet end. There was evidence indicating that the material had been subjected to periods of heating and cooling but the precise temperature to which the material had previously been heated could not be identified. The material did not appear to be melted. Whilst the piece of plastic was found lodged in the P3 line near the compressor plenum, an area which is normally subjected to high temperatures, it is likely that the plastic was dislodged during the impact sequence from a position nearer to the fuel control unit where temperatures are considerably lower and in which the plastic would have remained unaffected by the ambient temperatures. Survival aspects Considering the degree of injury sustained by the occupants, g-load peaks experienced during the accident sequence were probably low. The accident survivability was further aided by the fact that the cockpit survivable space was not reduced through fuselage deformation or penetration by any part of the structure. The pilot's seat was fitted with a Pacific Scientific MA-2 inertia reel. The harness reel control assembly lever was found in a manually locked position and the reel was immobilised as expected; however, it remained immobilised when re-positioned to the automatic reel-in position. Examination of the control assembly mechanism revealed corrosion and foreign material around the manual and automatic locking mechanism, resulting in restricted movement of the mechanism.
Accident investigation:
|
| |
Investigating agency: | BASI |
Report number: | |
Status: | Investigation completed |
Duration: | |
Download report: | Final report |
|
Sources:
https://www.atsb.gov.au/publications/investigation_reports/1996/aair/199600323/ https://www.atsb.gov.au/media/4931549/199600323.pdf Revision history:
Date/time | Contributor | Updates |
17-Apr-2018 12:01 |
Pineapple |
Added |
The Aviation Safety Network is an exclusive service provided by:
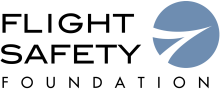
CONNECT WITH US:
©2024 Flight Safety Foundation