ASN Wikibase Occurrence # 233343
This information is added by users of ASN. Neither ASN nor the Flight Safety Foundation are responsible for the completeness or correctness of this information.
If you feel this information is incomplete or incorrect, you can
submit corrected information.
Date: | Saturday 15 February 2020 |
Time: | 08:42 LT |
Type: | Airbus A319-132 |
Owner/operator: | Spirit Airlines Inc |
Registration: | N521NK |
MSN: | 2797 |
Year of manufacture: | 2006 |
Total airframe hrs: | 44894 hours |
Engine model: | IAE V2524-A5 |
Fatalities: | Fatalities: 0 / Occupants: 117 |
Aircraft damage: | None |
Category: | Serious incident |
Location: | Sacramento International Airport, CA (SMF/KSMF) -
United States of America
|
Phase: | Approach |
Nature: | Passenger - Scheduled |
Departure airport: | Las Vegas-Harry Reid International Airport, NV (LAS/KLAS) |
Destination airport: | Sacramento International Airport, CA (SMF/KSMF) |
Investigating agency: | NTSB |
Confidence Rating: | Accident investigation report completed and information captured |
Narrative:Spirit Airlines Flight 1818, an Airbus A319-132, N521NK, experienced a fault with both engine integrated drive generators (IDG) while on approach to the Sacramento International Airport (SMF),
Sacramento, California.
This incident occurred when a Spirit Airlines Airbus A319 experienced a fault with both engine integrated drive generators (IDG) while on approach to the Sacramento International Airport (SMF), Sacramento, California. These faults resulted in the loss of electrical power supplied to both electrical networks (AC BUS 1 and AC BUS 2) leading to the loss of several flight deck displays and systems. Upon the dual loss of power, the ram air turbine (RAT) automatically extended and began driving the emergency generator to provide electrical power to vital services. The airplane landed without further incident, was towed to the gate and passengers deplaned normally.
A review of the airplane's maintenance records found that the airplane had experienced a similar dual loss of power event during an approach into the Hartsfield-Jackson Atlanta airport (KALT), Atlanta, Georgia on the previous day. The airplane had also experienced a similar loss of power on three different occasions on ground while performing single engine taxi after landing in January 2020.
Each engine's IDG was controlled by an independent digital computer called a generator control unit (GCU). One of its functions was to protect the IDG and its associated electrical network by monitoring and controlling the frequency and voltage output of its respected IDG. When the GCU detects a fault, it will isolate the IDG from the electrical network, and store the system fault data in its non-volatile memory (NVM). An amber fault message will also illuminate on the respective generator control push button switch indicating the channel is offline.
Post incident analysis of information from the airplane's GCU revealed that during the incident flight and during the dual loss of power event that occurred on the previous day, both GCU's recorded fault code 145. This information indicates that the frequency output for both the left and the right engine IDGs were outside of their specified design limits during the incident flight and on the previous day. Analysis of the data also revealed a similar out of limit frequency output from the left engine IDG when the airplane experienced the three loss of power events in January.
Examination and testing of the left engine IDG revealed that an internal component, a fixed cylinder block, was significantly worn beyond its design limits. Wear was observed in the gold-colored liners assembled inside of the bores of the cylinder block. The wear was uneven around the circumference and occurred close to either end of the bores, with the heaviest wear extending up from the bottom of the bores. The gold-colored liners were worn through in some areas in several bores, and silver-colored base metal was visible. The fixed cylinder block and pistons within IDG1 were replaced with serviceable original equipment manufacturer (OEM) parts and the IDG was re-tested. The IDG passed its tests indicating that the wear on the fixed cylinder block and pistons was the reason for the IDG failure during the event flight.
Examination of IDG2 revealed that only one of the cylinder bores of the fixed cylinder block was worn through in a similar fashion to the cylinder block from IDG1. Although testing of this IDG found that it exhibited a significant frequency modulation on its electrical output, the output was not outside of its specified design limit and therefore would not have triggered a fault code 145 to be recorded on the GCU. Nevertheless, several tests showed that the fault code 145 was almost triggered under the following test conditions: 1) A constant speed (or a slow sweep profile) between 6,100 RPM and 6,150 RPM, 2) A high IDG load that seems to increase slightly with the modulation amplitude.
Although Spirit Airlines maintenance had performed troubleshooting on the airplane after each of the previous loss of electrical power events, they were unable to determine any faults with the electrical system, including the IDGs. A review of their maintenance records found that the testing included a run-up of the engines to check electrical loads per their aircraft maintenance manual (AMM), and operational testing of the IDGs. According to Airbus, the introduction section of their A318/A319/A320/A321 troubleshooting manual (TSM) indicated that if an operator cannot find a fault symptom and/or fault isolation procedure necessary to ensure the continued airworthiness of the aircraft they should contact Airbus. Airbus indicated that they were not contacted by Spirit Airlines for assistance on these loss of electrical power events. It is likely that if Spirt Airlines maintenance had contacted Airbus for these loss of electrical power events, they may have identified fault code 145 on the Number 1 GCU and replaced its respective IDG prior to the February 15th event.
As a result of this incident, Airbus has improved their TSM by incorporating steps to direct maintenance towards a direct extraction of the post flight report (PFR) and troubleshooting data (TSD) from the GCUs.
Probable Cause: A worn component within each engine integrated drive generator (IDG) resulted in the loss of electrical power supplied to several flight deck displays and systems while on approach to landing. The component, a fixed cylinder block, had significant wearing of its reworked brass liners resulting in the IDGs producing a frequency output outside of their specified design limit.
Accident investigation:
|
| |
Investigating agency: | NTSB |
Report number: | ENG20LA016 |
Status: | Investigation completed |
Duration: | 2 years and 7 months |
Download report: | Final report |
|
Sources:
NTSB ENG20LA016
Location
Revision history:
Date/time | Contributor | Updates |
29-Feb-2020 07:50 |
harro |
Added |
The Aviation Safety Network is an exclusive service provided by:
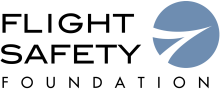
CONNECT WITH US:
©2024 Flight Safety Foundation