ASN Wikibase Occurrence # 284088
This information is added by users of ASN. Neither ASN nor the Flight Safety Foundation are responsible for the completeness or correctness of this information.
If you feel this information is incomplete or incorrect, you can
submit corrected information.
Date: | Monday 29 October 2007 |
Time: | 16:36 LT |
Type: | MD Helicopters MD 500E (369E) |
Owner/operator: | Columbus City Police |
Registration: | N556CP |
MSN: | 0567E |
Year of manufacture: | 2004 |
Total airframe hrs: | 3094 hours |
Engine model: | Rolls-Royce 250-C20B |
Fatalities: | Fatalities: 0 / Occupants: 2 |
Aircraft damage: | Substantial |
Category: | Accident |
Location: | Columbus, OH -
United States of America
|
Phase: | Unknown |
Nature: | Unknown |
Departure airport: | Columbus, OH (OH52) |
Destination airport: | |
Investigating agency: | NTSB |
Confidence Rating: | Accident investigation report completed and information captured |
Narrative:The public-use helicopter was on a routine patrol flight when it experienced a sudden loss of engine power. The pilot performed an autorotation to an island peninsula located on a nearby river. The landing flare eliminated the helicopter's forward movement and touchdown was made on both skids. The helicopter remained upright momentarily before the right skid sank down into the muddy terrain. The helicopter subsequently rolled over onto its right side. The vertical stabilizer, tail boom, and all five main rotor blades were substantially damaged.
Postaccident engine inspection revealed that one airfoil (blade) had separated near the rim of the fourth-stage turbine wheel. The fracture initiated at the airfoil trailing edge root fillet and propagated in high-cycle fatigue until finally separating in mechanical overload. No machining anomalies were noted at the fracture origin area. Scanning electron microscopy analysis of all the observed fractures revealed no metallurgical or geometric anomalies at the fracture origin. Material properties near the fracture origin were consistent with the engine manufacturer's specifications. All additional damage throughout the engine was secondary to the airfoil separation from the fourth-stage turbine wheel.
The fourth-stage turbine wheel had accumulated 2,918.7 hours and 1,718 cycles since new. The turbine wheel was the current design used in the Series II "Enhanced" Power Turbine assembly. The enhanced power turbine design was used in a variety of fixed-wing and rotorcraft aircraft. There have been five known airfoil separations with the enhanced power turbine design, four of which occurred the same model aircraft.
A root cause investigation revealed the possibility of a higher stress state in the turbine wheel airfoil trailing edge root fillet than was originally modeled when the turbine wheel was released in 1999. This elevated stress state, which was modeled to occur during engine startup, was the result of a thermal gradient in the turbine airfoil geometry. This thermal gradient could result in a residual stress condition in the airfoil hub trailing edge, and potentially lead to the initiation of fatigue crack. If a crack was initiated, operation of the engine in a wheel resonance mode may propagate the existing crack in high-cycle fatigue and ultimately result in an airfoil separation. The wheel resonance mode occurred during sustained engine operations between 75 and 88 percent N2. This engine speed avoidance range had been previously communicated to operators in the form of an alert bulletin that was originally issued in December 2006, approximately 10 months before the accident. According to the helicopter operator, upon the bulletin's release, they had adhered to the specified speed avoidance range during all flight and maintenance operations.
In response to this accident and other similar wheel failures, the engine manufacturer issued an alert maintenance bulletin that required the one-time inspection of the third and fourth stage turbine wheels for possible airfoil cracks. The bulletin was applicable to McDonnell Douglas Helicopter models equipped with a Series II "Enhanced" Power Turbine Design. The bulletin stated that prolonged engine operation in the 75-88 percent N2 speed avoidance range could result in airfoil fracture and possible separation. The inspection was to be completed at the next 1,750 hour overhaul and required the removal of the applicable turbine wheels for fluorescent-penetrant and visual inspections. The bulletin called for the replacement of any wheel that contained a fracture of an airfoil trailing edge near the rim where the fillet engages the trailing edge.
To mitigate future turbine wheel airfoil fractures, the engine manufacturer has redesigned the turbine wheel to adequately accommodate the higher thermal gradient encountered during engine startup. As of January 2011, the required design changes have been approved and the new wheel design will be deployed during the fourth quarter of 2011.
Probable Cause: The inadequate turbine wheel design that led to a turbine airfoil (blade) failure/separation, resulting in the loss of engine power.
Accident investigation:
|
| |
Investigating agency: | NTSB |
Report number: | CHI08GA028 |
Status: | Investigation completed |
Duration: | 3 years and 6 months |
Download report: | Final report |
|
Sources:
NTSB CHI08GA028
Revision history:
Date/time | Contributor | Updates |
30-Sep-2022 07:47 |
ASN Update Bot |
Added |
31-May-2023 05:13 |
Ron Averes |
Updated |
The Aviation Safety Network is an exclusive service provided by:
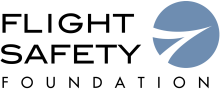
CONNECT WITH US:
©2024 Flight Safety Foundation