ASN Wikibase Occurrence # 294532
This information is added by users of ASN. Neither ASN nor the Flight Safety Foundation are responsible for the completeness or correctness of this information.
If you feel this information is incomplete or incorrect, you can
submit corrected information.
Date: | Wednesday 8 September 2004 |
Time: | 16:00 LT |
Type: | Mcdonnell Douglas MD 900 |
Owner/operator: | Md Helicopters Inc. |
Registration: | N9016W |
MSN: | 900-00016 |
Year of manufacture: | 1995 |
Total airframe hrs: | 1687 hours |
Engine model: | Pratt & Whitney 206A |
Fatalities: | Fatalities: 0 / Occupants: 1 |
Aircraft damage: | Substantial |
Category: | Accident |
Location: | Mesa, Arizona -
United States of America
|
Phase: | Unknown |
Nature: | Test |
Departure airport: | Mesa, AZ (AZ81) |
Destination airport: | Mesa, AZ (AZ81) |
Investigating agency: | NTSB |
Confidence Rating: | Accident investigation report completed and information captured |
Narrative:The helicopter experienced a NOTAR (no tail rotor) fan failure during the initial climb from the airport and made a subsequent hard landing. Immediately after takeoff, about 30 to 40 feet above ground level (agl), the helicopter began to vibrate. The pilot lowered the collective to the full down position, and the helicopter touched down about 30 to 40 knots ground speed. Upon touchdown, the pilot had difficulty maintaining directional control and the helicopter slid about 300 feet across terrain. The helicopter's NOTAR anti-torque yaw control system utilizes a transmission driven fan with variable pitch blades to supply air to circulation control slots on the tail boom and a pilot controlled directional jet thruster nozzle. Movement of the anti-torque control pedals changes the fan blade pitch to produce more or less airflow to the circulation control slots and the anti-torque thruster nozzle. As the pedals are displaced from center toward either extreme of travel, the airflow increases or decreases proportionally. A post-accident examination of the NOTAR fan system revealed that one of the thirteen Tension-Torsion (T-T) straps located on the variable-pitch fan assembly had failed. The failed strap had accumulated about 1,694 hours of time in service, though the design safe life for the strap was 2,500 hours of time in service. An examination of the strap revealed that it had fractured as a result of the progressive failure of its reinforcement fibers. This progressive fiber failure gradually degraded the strap's integrity until it could no longer support normal in-service tensile loads. In normal operation, the T-T straps are exposed to tensile loads due to the centrifugal force induced by the blade rotation about the anti-torque fan axis. The straps are additionally exposed to torsional loads about their longitudinal axis as the blade pitch is changed. The point-symmetric locations of the failure areas were consistent with loading that would occur as the strap was twisted with limited centrifugal force loads present; the twisting direction corresponds to an increase in blade pitch. The Safety Board Materials Laboratory performed load analyses of the straps, revealing that when the strap is twisted without the presence of centrifugal force, portions of the fiber reinforced region of the strap are subjected to compression and transverse shear stresses. Furthermore, the compression and transverse shear stresses are highest in the locations where the subject strap failed. When the anti-torque fan is rotated at speeds less than an approximate 75 percent of maximum power, compression, and transverse shear stresses can develop in the straps when the blade pitch is adjusted. Additionally, with no fan rotation (and therefore no centrifugal force) critical buckling strains on the strap's fibers can be achieved by increasing the blade pitch to near the design limits. This could plausibly occur during a preflight inspection when the pilot checks pedal control surface movement prior to starting the engine. All T-T strap load and fatigue tests preformed by the helicopter manufacturer incorporate centrifugal force loads, and therefore, do not test the full load spectrum.
Probable Cause: fracture of a Tension-Torsion strap in the anti-torque fan due to progressive fiber failure of the composite strap material from compression and/or transverse shear stresses that occurred with repeated manipulation of the cockpit anti-torque control pedals without the fan operating at full rpm. A factor in the accident was the helicopter manufacturer's inadequate fatigue and load testing on the strap.
Accident investigation:
|
| |
Investigating agency: | NTSB |
Report number: | LAX04LA333 |
Status: | Investigation completed |
Duration: | 1 year and 8 months |
Download report: | Final report |
|
Sources:
NTSB LAX04LA333
Revision history:
Date/time | Contributor | Updates |
11-Oct-2022 19:17 |
ASN Update Bot |
Added |
The Aviation Safety Network is an exclusive service provided by:
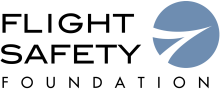
CONNECT WITH US:
©2024 Flight Safety Foundation