ASN Wikibase Occurrence # 385547
This information is added by users of ASN. Neither ASN nor the Flight Safety Foundation are responsible for the completeness or correctness of this information.
If you feel this information is incomplete or incorrect, you can
submit corrected information.
Date: | Wednesday 25 July 2001 |
Time: | 02:50 LT |
Type: | McDonnell Douglas MD 520N |
Owner/operator: | Los Angeles County Sheriff's Department |
Registration: | N953SD |
MSN: | LN070 |
Total airframe hrs: | 5852 hours |
Engine model: | Allison 250-C20R |
Fatalities: | Fatalities: 0 / Occupants: 2 |
Aircraft damage: | Minor |
Category: | Serious incident |
Location: | Los Angeles, CA -
United States of America
|
Phase: | Initial climb |
Nature: | Unknown |
Departure airport: | Los Angeles International Airport, CA (LAX/KLAX) |
Destination airport: | Long Beach Airport, CA (LGB/KLGB) |
Investigating agency: | NTSB |
Confidence Rating: | Accident investigation report completed and information captured |
Narrative:The helicopter was climbing eastbound after liftoff and was passing 300 feet agl when the crew heard a loud squeal and felt a high frequency vibration in the airframe and in the antitorque control pedals. The pilot executed a 180-degree turn and landed back at the helipad. The NOTAR fan drive system was disassembled for examination. The Aft Tube Assembly transmits antitorque pedal inputs to the NOTAR fan blade pitch change mechanism and moves fore and aft through the hollow rotating fan drive shaft. The tube does not rotate. Three distinct areas of circumferential scoring were noted on the tube; one in the center at roughly the middle of the drive shaft, and one at each end of the tube corresponding to locations just within the fan drive gear box on the forward end and just inside of the fan assembly. The pilot reported that during an earlier flight in the accident helicopter, the antitorque pedals seemed to stick or slightly bind with 2 inches of right pedal displacement. The pilot stated that this was an annoying problem that regularly occurred with all the 520N's in their fleet, and that the maintenance department typically cleared it up by cleaning (lightly sanding) a Teflon coated sliding tube in the NOTAR fan assembly. According to the pilot, dirt and oil would get on this sliding tube and cause it to bind in the housing, and the mechanics would simply clean this tube to resolve the problem. Maintenance department mechanics confirmed that the pedal-sticking problem typically involved foreign material on the aft tubes' Teflon coated pitch slider, and that they routinely resolved the discrepancies by removing the aft tube and lightly sanding the Teflon coating with fine sand paper. With the exception of the aft tube and it's associated pitch slider shaft, extensive examinations and tests of the NOTAR system components revealed no anomalies that could be related to the vibratory event. Examination of the pitch slider shaft found numerous, very fine, axial scratches on the surface, and measurements found that the outer diameter had been reduced by up to 0.014 inch from the manufacturer's specified constant 0.818 inch ( 0.001 inch). The hand sanding of the liner resulted in axial surface scratches and a variable shaft outer diameter that was smaller than that required by the MDHI specification. The decreased and variable liner OD degraded the ability to isolate the aft tube assembly from drive system vibrations. The bending mode natural frequencies of the aft tube assembly were assessed to be 65, 220, and 450 Hz. Initial MDHI estimates stated that the first bending mode natural frequency of the aft tube assembly was 94 Hz. The operational rotor speed of the MDHI 520N helicopter is 7.95 Hz, and the operational NOTAR fan and drive system rotational speed is 89.4 Hz. While in comparison, the measured first bending mode natural frequency of the aft tube assembly of 65 Hz offers a margin of 24.4 Hz under the 89.4 Hz operating speed of the NOTAR fan drive syste;, the actual natural frequency may be higher and result in a smaller margin. The investigation determined that a maintenance practice of sanding the Teflon coated pitch slider tube in the NOTAR assembly resulted in excessive clearance between the antitorque system components. This excessive clearance allowed a vibration to occur in those components resulting in the noise and airframe vibrations noted by the pilots.
Probable Cause: the excitation of the first bending mode natural frequency of the aft tube assembly that is installed through the rotating NOTAR fan drive system. Contributing factors to the incident included the operator's maintenance practice of hand-sanding the pitch slider component of the NOTAR fan system.
Accident investigation:
|
| |
Investigating agency: | NTSB |
Report number: | LAX01IA262 |
Status: | Investigation completed |
Duration: | 2 years and 6 months |
Download report: | Final report |
|
Sources:
NTSB LAX01IA262
Location
Revision history:
Date/time | Contributor | Updates |
05-Apr-2024 05:21 |
ASN Update Bot |
Added |
The Aviation Safety Network is an exclusive service provided by:
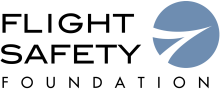
CONNECT WITH US:
©2024 Flight Safety Foundation